Spent a bit of time on the 3 last night-
Fixed the sidewards install of the passenger headlight. You gotta wonder what people are thinking...
The sheetmetal part of the windshield frame at the top of the glass was bent inward about 1/2" or so, and had a deeper dent on the driver's side from falling on to the wood hood blocks.
I decided to try and straighten it out. I had a piece of tube steel that I clamped to the top outside of the frame.
And a piece of 2x on the inside with a clamp in the middle. I was able to use the middle clamp to rotate downward and push out the bend in the frame opening.
I did the same thing at the deeper dent spot with a smaller block, and some light hammering, and it came out pretty good.
After, it's mostly straight, and probably the straightest part of the jeep now
I made a CAD template of the glass, to take to the glass shop for to get a new piece cut.
A face only a jeeper could love.
I ordered a master rebuild kit for the Carter WO carb. It has seen better days, so decided to give it a complete go through.
And, the steering box parts arrived, so we will be tearing town the Ross box for a rebuild. I can't wait to see what is inside, there is so much play in there not sure how it even works at this point. There must be some serious wear on the sector shaft or worm gear.
More to come...
Pete
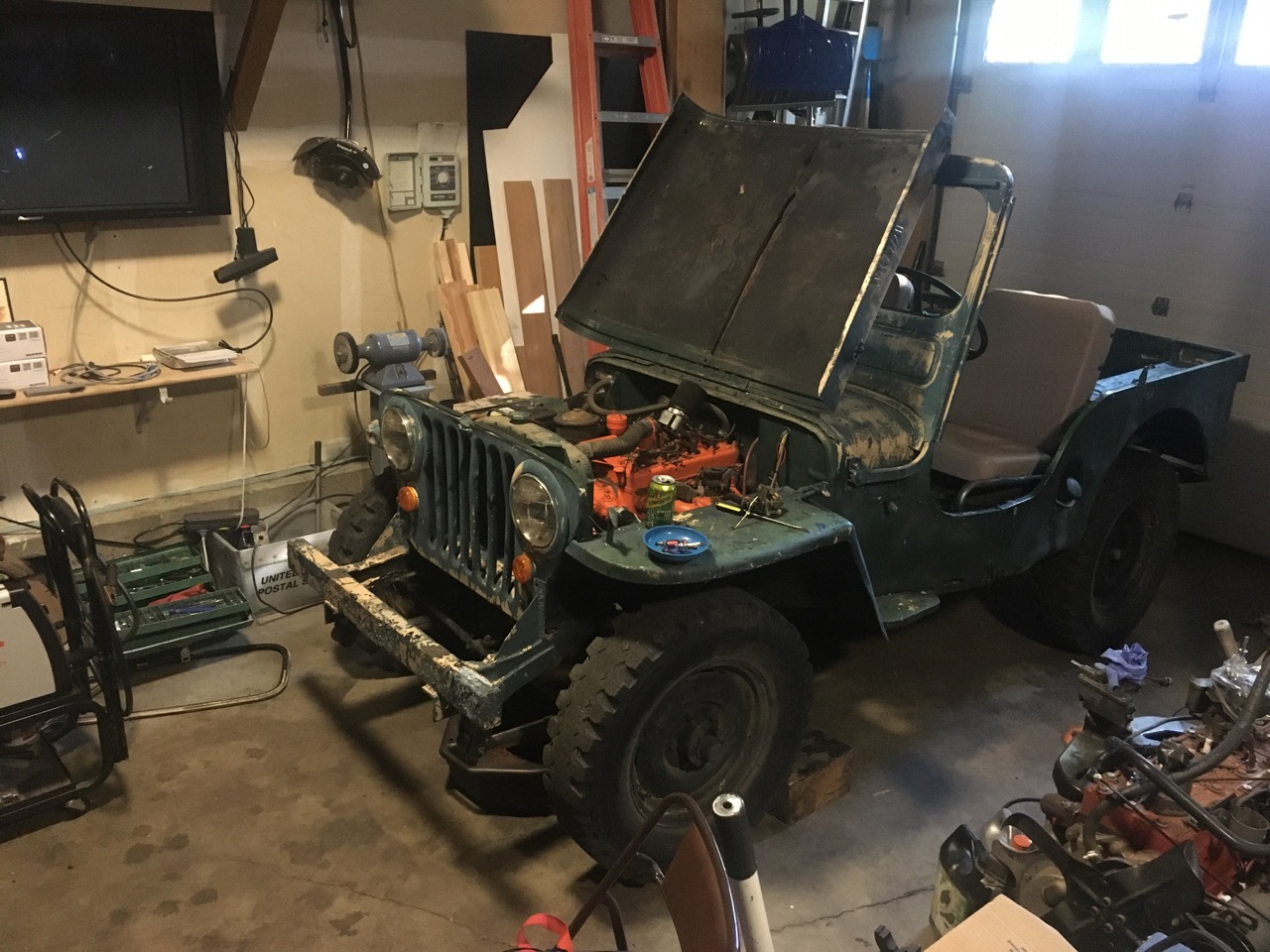
Fixed the sidewards install of the passenger headlight. You gotta wonder what people are thinking...
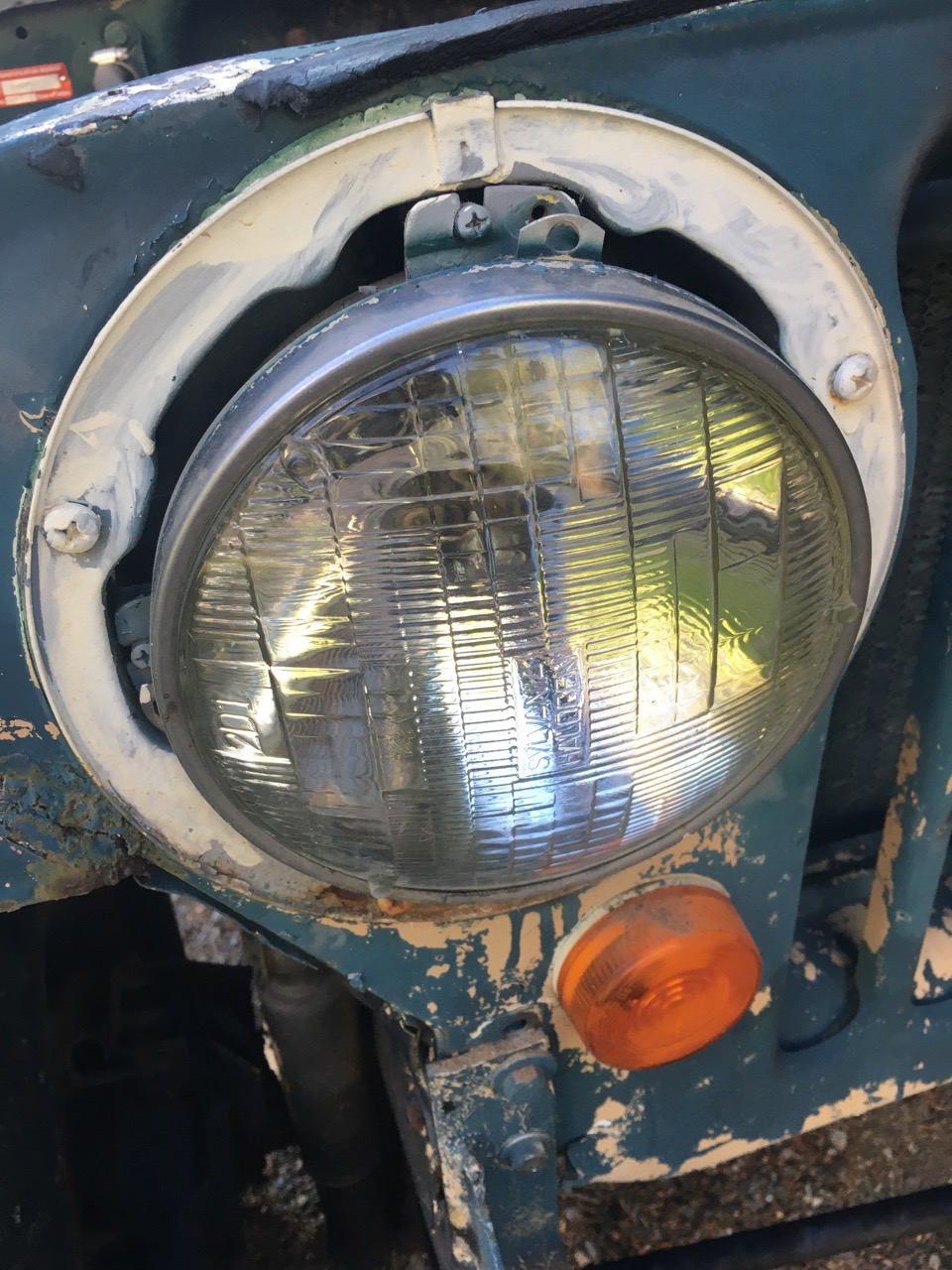
The sheetmetal part of the windshield frame at the top of the glass was bent inward about 1/2" or so, and had a deeper dent on the driver's side from falling on to the wood hood blocks.

I decided to try and straighten it out. I had a piece of tube steel that I clamped to the top outside of the frame.
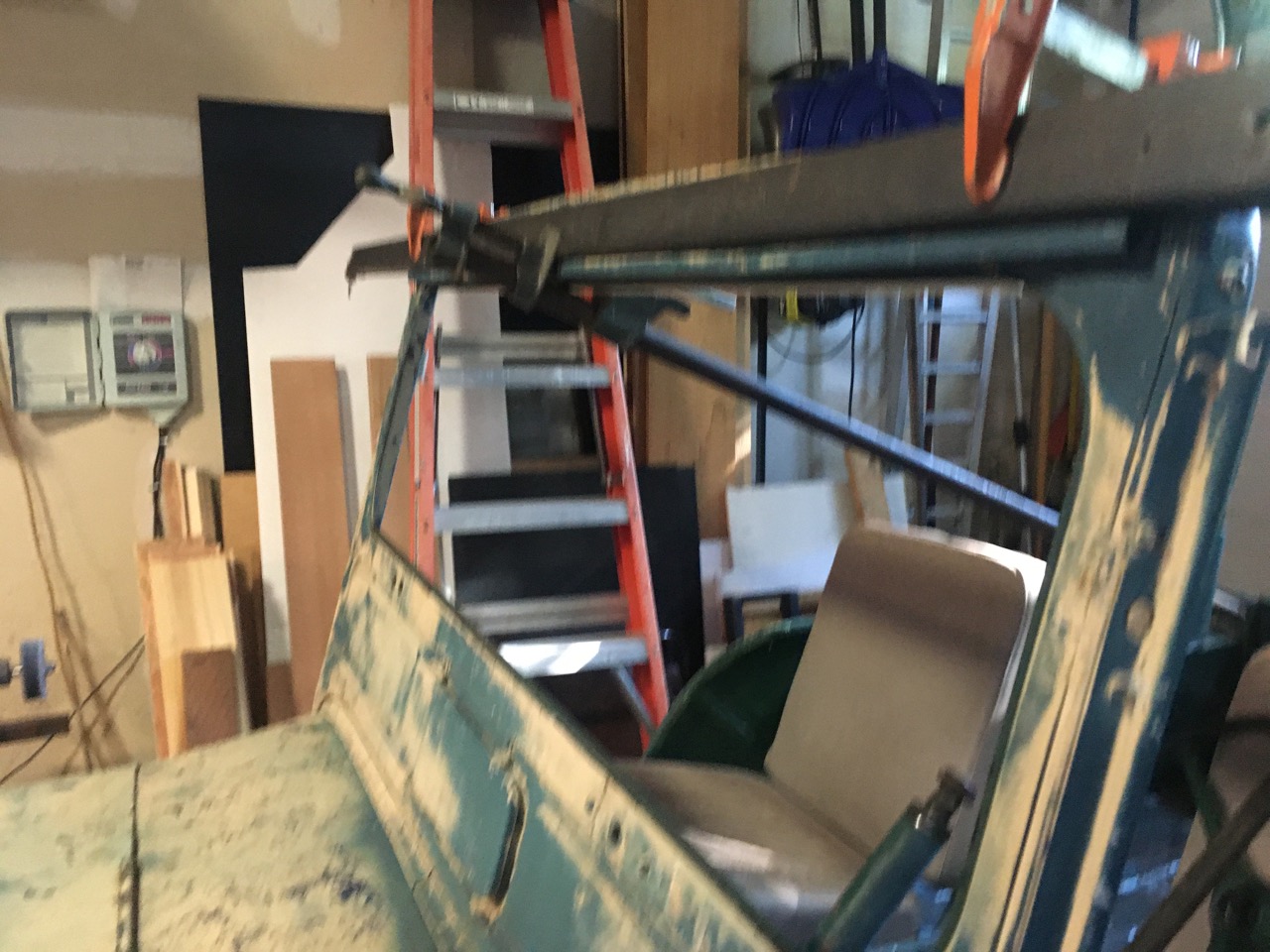
And a piece of 2x on the inside with a clamp in the middle. I was able to use the middle clamp to rotate downward and push out the bend in the frame opening.
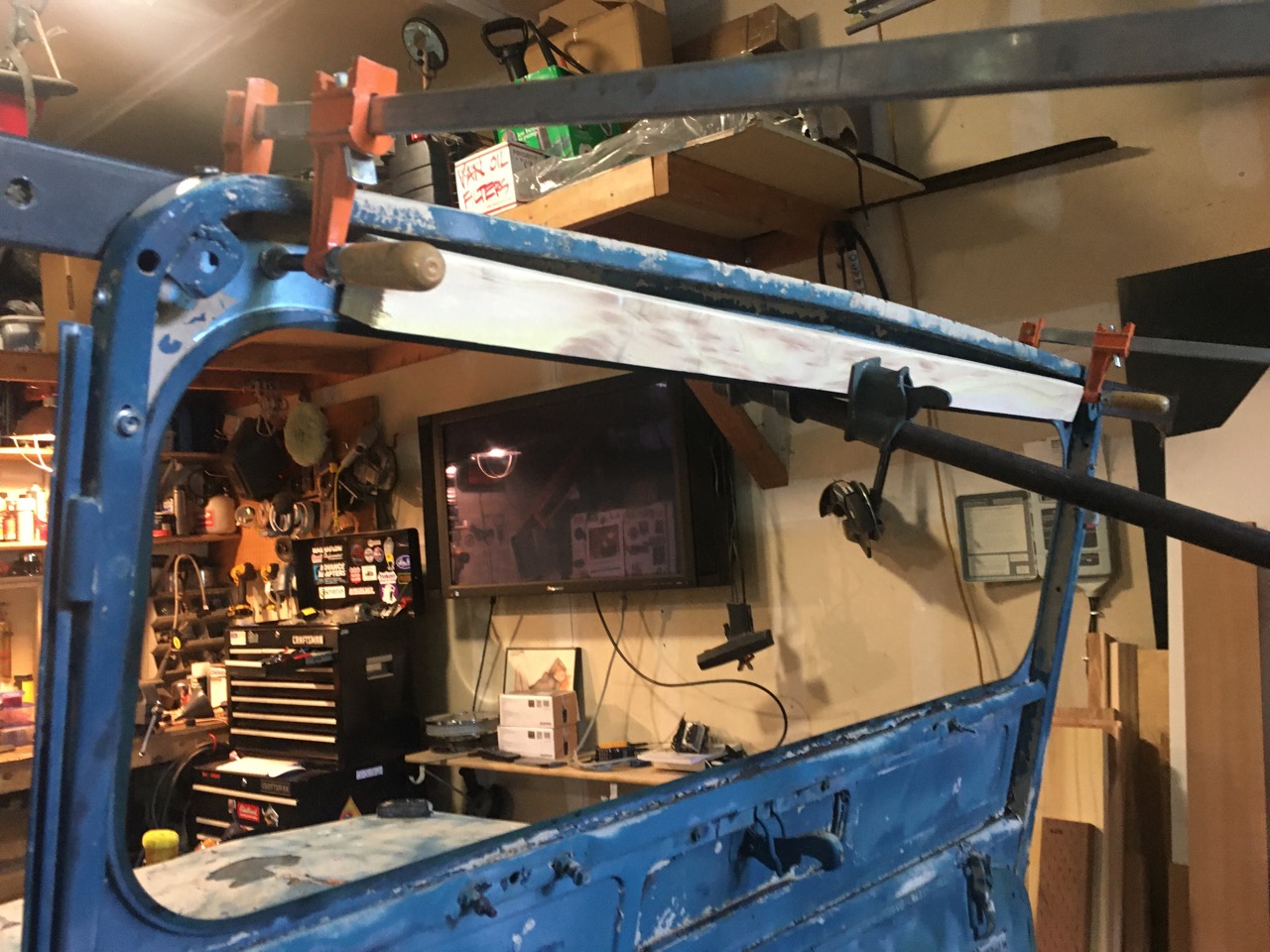
I did the same thing at the deeper dent spot with a smaller block, and some light hammering, and it came out pretty good.
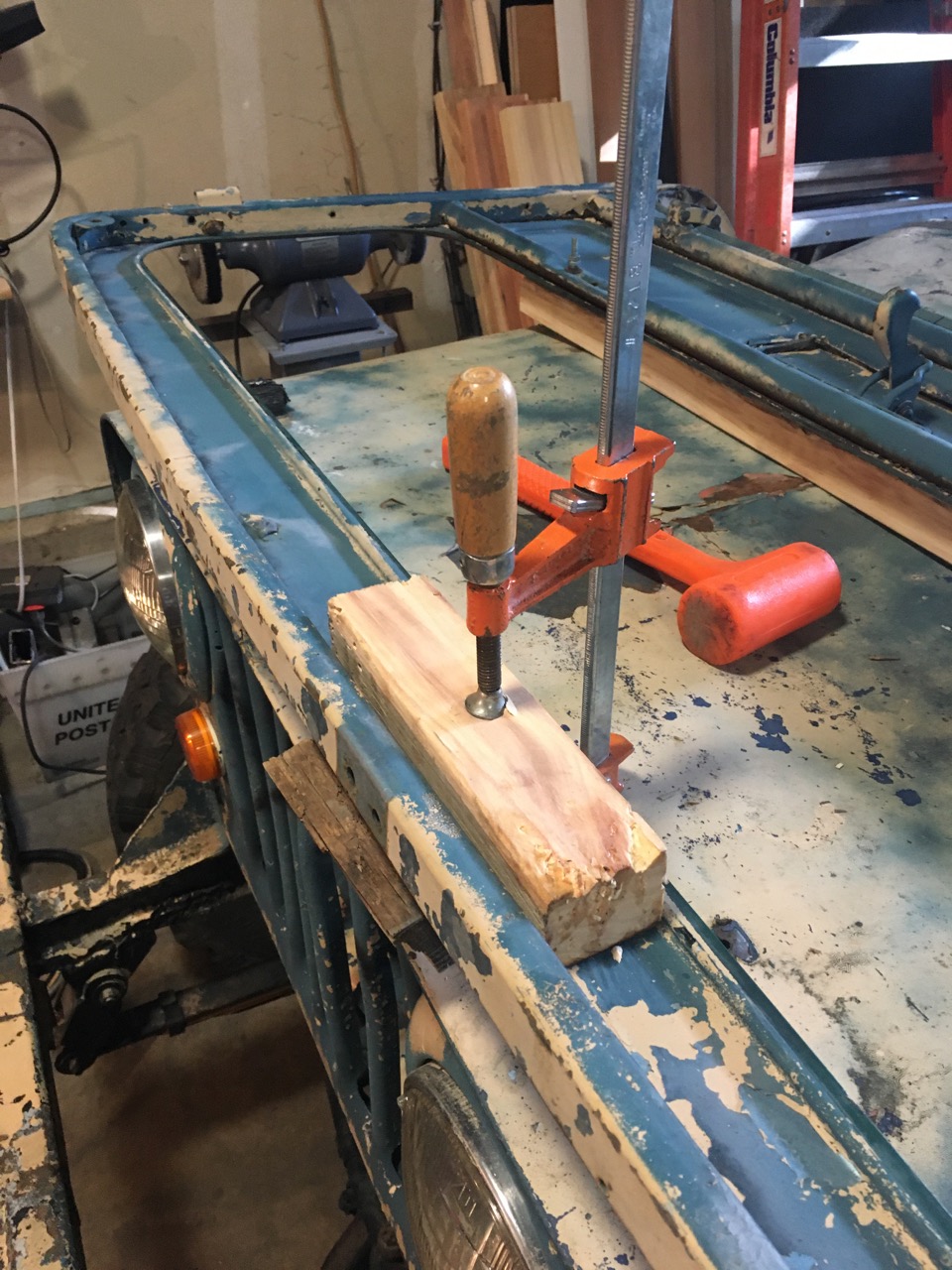
After, it's mostly straight, and probably the straightest part of the jeep now
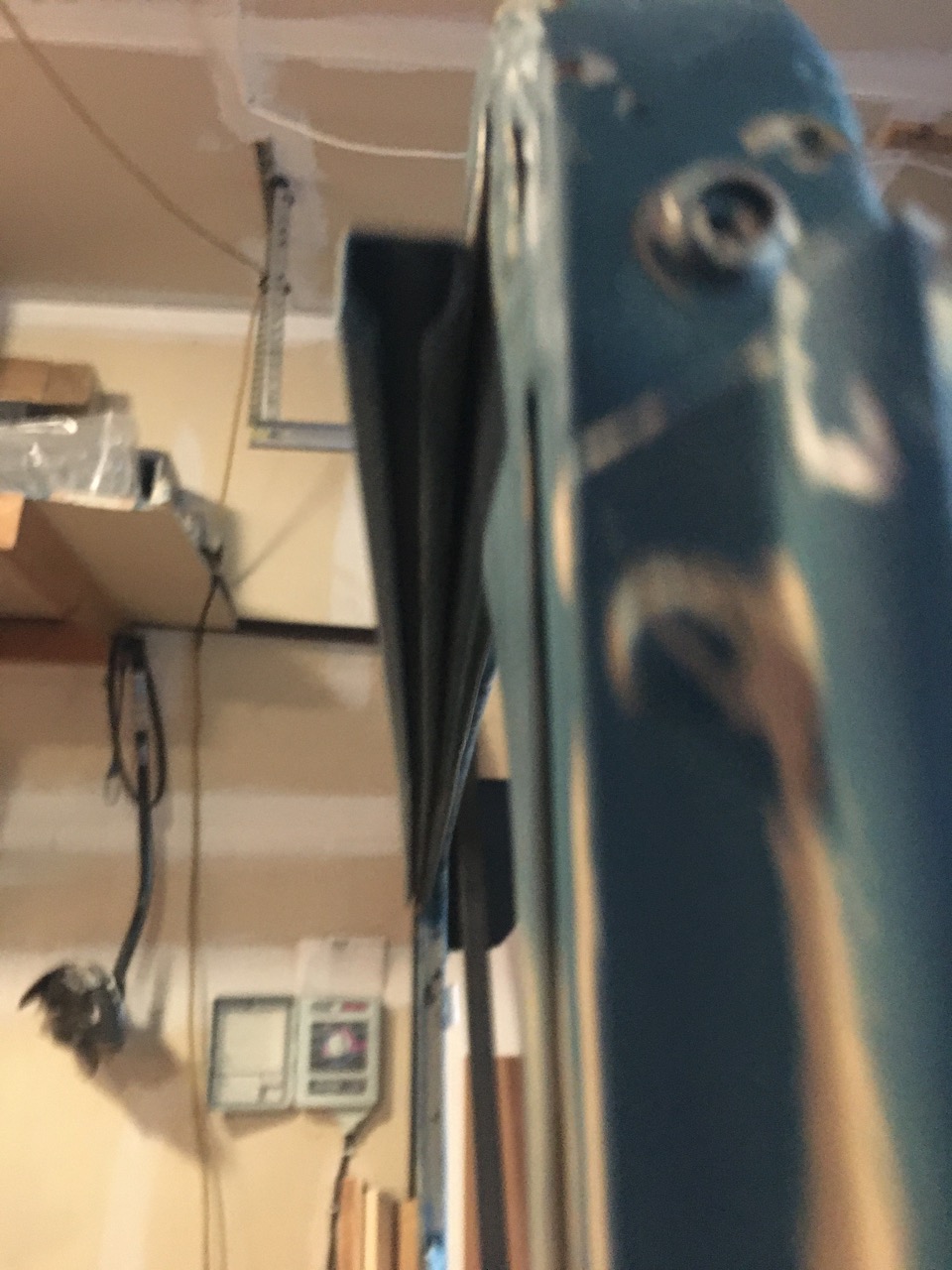
I made a CAD template of the glass, to take to the glass shop for to get a new piece cut.
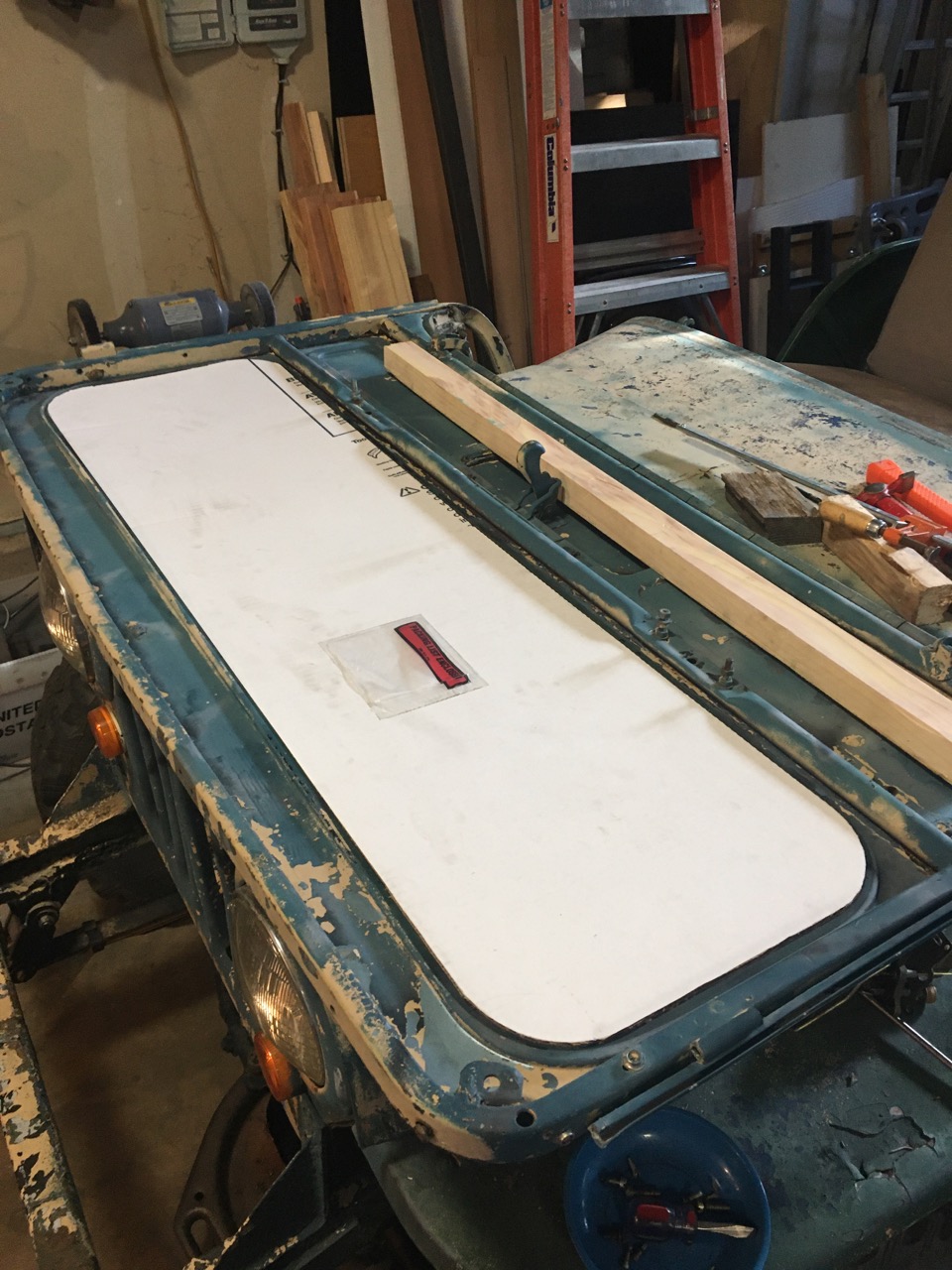
A face only a jeeper could love.
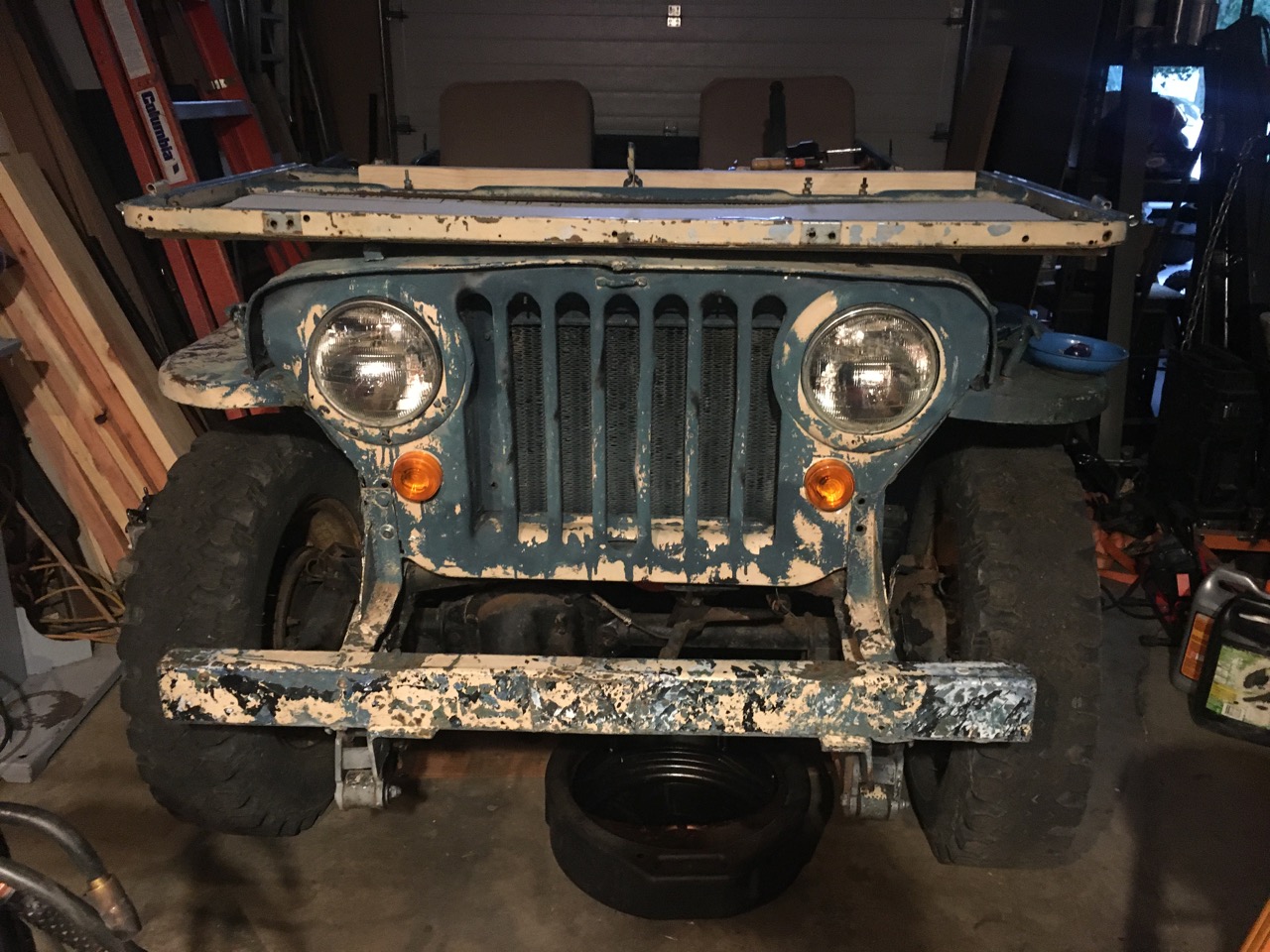
I ordered a master rebuild kit for the Carter WO carb. It has seen better days, so decided to give it a complete go through.
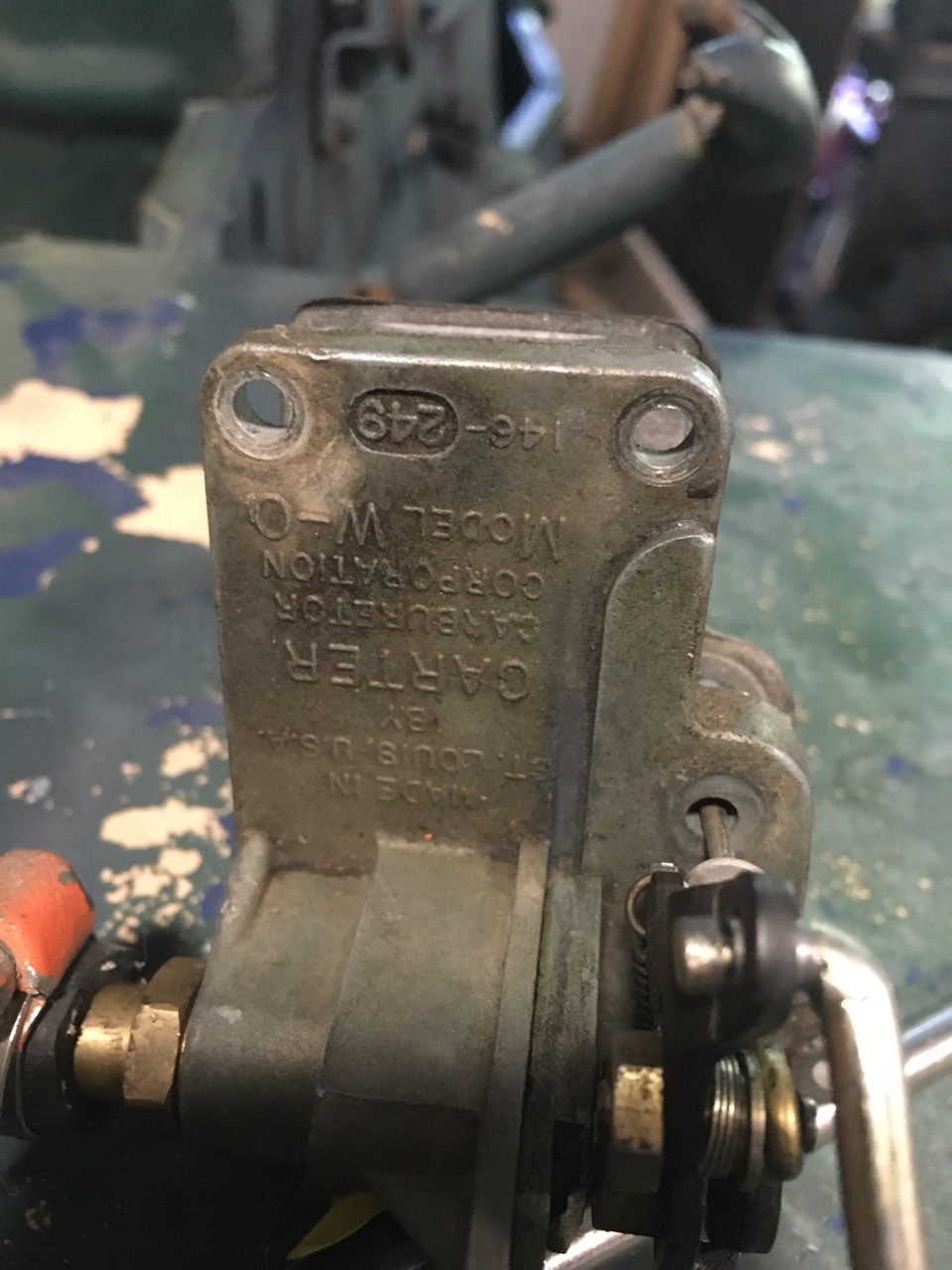
And, the steering box parts arrived, so we will be tearing town the Ross box for a rebuild. I can't wait to see what is inside, there is so much play in there not sure how it even works at this point. There must be some serious wear on the sector shaft or worm gear.

More to come...
Pete