Vintage Don
Well Oiled
This seems like kind of a small job, after having done the entire cab floor, and later the entire bed floor along with part of the side walls. But when I did those jobs, I had a good buddy helping me on and off - and he is a better fabricator and welder than I am. His guidance and help got me through it pretty well.
Well, since we're all in isolation these days, I decided I was going to try to do this job on my own - and it scared me, I honestly figured I would screw it up, cut it all back out - and wait for normal times to return and get him to hold my hand again. Haha
But I made it, and was all puffed up proud of myself. I truly did not expect to get a decent result. Not saying it's great, but I think it'll do.
Rotted door bottoms are apparently a pretty common problem, and mine are bad across the bottoms on both sides. This is looking up at the bottom of the passenger side, which is actually the better of the two. I've got my chalk cut lines already drawn in here, where the metal is definitely rotted.
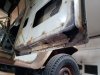
So getting that out of there is more complicated than I expected... The outer door skin has tabs (circled in red below) that bend around from the outside and grab that inner piece, in a crimp. Also a few spot welds. So you have to v-e-r-y carefully pry that open, and drill out the welds - being very careful not to mess up the outer door skin.
Finally getting that stuff cut out (hours) revealed how rotted out the OUTER skin actually was! (arrow) Now, I was really worried.
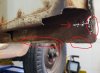
And it was up into the lower of those 3 horizontal "ribs" that run across the bottom of the doors (yikes!) which made it all the more challenging, to try to match all that up and look factory.
At first, I was going to try to just piece it in, and save the outer perimeter shape for a guide for what I was trying to build. But I finally decided the whole corner needed to come off, to make a strong enough repair and to have solid metal to meet up to.
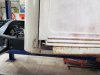
(I ended up cutting it farther forward after that photo)
This meant I had to recreate those little flaps to crimp, including where they go around the door's corner radius, where it is just a tiny little rolled lip. And - recreate part of the bottom and end of the "rib" I had to cut into. I don't know how to do this kind of stuff!!!
I started with my usual plan of action, trying to make the patch that would be required out of card stock first, to understand what the tabs needed to look like.
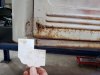
And then I just went for it. Used everything I could think of to shape that piece and get a respectable result. Vise, pliers, hammers, anvil, chisel tips, pipe... But a few hours later, I actually had a reasonable looking patch made.
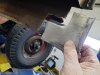
And it fit pretty well. Much to my surprise!
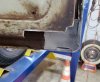
So then it was a matter of welding and grinding. Lots of other holes burnt through, even at lowest heat. Just kept "chasing the rabbits" until I was pretty well sealed up.
This (below) is just after the first rough grinding. I'l weld on it some more, chase some more rabbits, and get the final grinding looking more finished later. Ran out of time this evening.
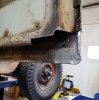
And the door fits and closes fine. Gaps are about the same as they were. So old Vintage Don is all proud tonight!
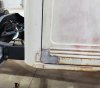
There are 5 or 6 other areas like this to deal with. The first one is right there just behind this new patch, on the lower end of the B pillar there, as you can see.
But I think tomorrow before I go after those areas, I will try to fabricate the long bottom piece - the door "floor" - and see what that looks like.
Well, since we're all in isolation these days, I decided I was going to try to do this job on my own - and it scared me, I honestly figured I would screw it up, cut it all back out - and wait for normal times to return and get him to hold my hand again. Haha
But I made it, and was all puffed up proud of myself. I truly did not expect to get a decent result. Not saying it's great, but I think it'll do.
Rotted door bottoms are apparently a pretty common problem, and mine are bad across the bottoms on both sides. This is looking up at the bottom of the passenger side, which is actually the better of the two. I've got my chalk cut lines already drawn in here, where the metal is definitely rotted.
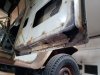
So getting that out of there is more complicated than I expected... The outer door skin has tabs (circled in red below) that bend around from the outside and grab that inner piece, in a crimp. Also a few spot welds. So you have to v-e-r-y carefully pry that open, and drill out the welds - being very careful not to mess up the outer door skin.
Finally getting that stuff cut out (hours) revealed how rotted out the OUTER skin actually was! (arrow) Now, I was really worried.
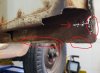
And it was up into the lower of those 3 horizontal "ribs" that run across the bottom of the doors (yikes!) which made it all the more challenging, to try to match all that up and look factory.
At first, I was going to try to just piece it in, and save the outer perimeter shape for a guide for what I was trying to build. But I finally decided the whole corner needed to come off, to make a strong enough repair and to have solid metal to meet up to.
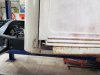
(I ended up cutting it farther forward after that photo)
This meant I had to recreate those little flaps to crimp, including where they go around the door's corner radius, where it is just a tiny little rolled lip. And - recreate part of the bottom and end of the "rib" I had to cut into. I don't know how to do this kind of stuff!!!
I started with my usual plan of action, trying to make the patch that would be required out of card stock first, to understand what the tabs needed to look like.
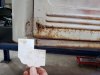
And then I just went for it. Used everything I could think of to shape that piece and get a respectable result. Vise, pliers, hammers, anvil, chisel tips, pipe... But a few hours later, I actually had a reasonable looking patch made.
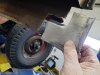
And it fit pretty well. Much to my surprise!
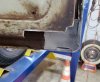
So then it was a matter of welding and grinding. Lots of other holes burnt through, even at lowest heat. Just kept "chasing the rabbits" until I was pretty well sealed up.
This (below) is just after the first rough grinding. I'l weld on it some more, chase some more rabbits, and get the final grinding looking more finished later. Ran out of time this evening.
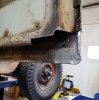
And the door fits and closes fine. Gaps are about the same as they were. So old Vintage Don is all proud tonight!
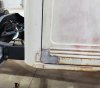
There are 5 or 6 other areas like this to deal with. The first one is right there just behind this new patch, on the lower end of the B pillar there, as you can see.
But I think tomorrow before I go after those areas, I will try to fabricate the long bottom piece - the door "floor" - and see what that looks like.