WA7OPY
Well Oiled
Well the build has started after 2 years, flywheel and bell housing ring started life as a 16 inch piece of 2 inch plate. To save money the plate was cut thru and made a 16x13 doughnut and a 12 inch drop for the flywheel, not a easy thing to do but it is done. The bell-housing is round so I machined a bolt up ring to weld the rest of the bell housing to. It going to take a while but the first step is making the engine, clutch and trany into one working piece.The engine is a c240 Isuzu non epa, 75 hp just slightly larger than the L134 willys and about the same weight...Phil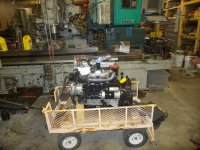
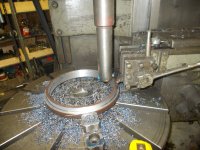
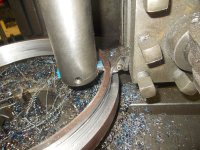
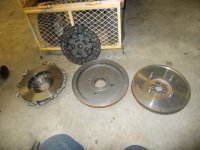

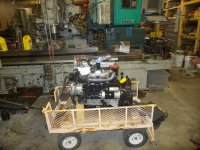
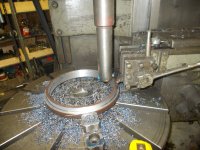
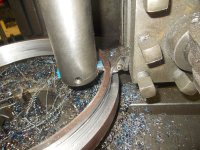
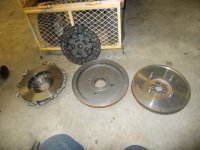

Last edited: