rocket
Well Oiled
I started to post about this re-purposing project over in the Motorcycle section but I think it needs it's own build page.
I broke my Right Achilles Tendon 2+ years ago and have not ridden any of my 4 BSA motorcycles since. They start easy with the kick starter when warm, but after sitting a few months, they can be a bear to start. Here are a few examples. Most on the market sell in the $1,000.00 range.



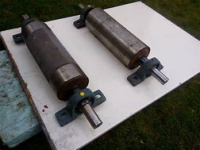
This old tread mill was being thrown out by my daughter during one of her last home sales. I drug it home and it's been in my barn for several years. I left the upper portion in the dumpster and just brought home the roller base.
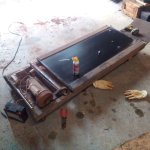
Moving on to the disassembly I discovered the motor is 125 VDC and I think it had died a terrible death. So the only thing I decided to use was the rollers and shafts. They are a 2.5" rollers, that ring like a driveshaft tube. They use a 3/4" shaft with internal bearings, So unlike most of the M/C starters, I won't be using Pillow Block , or flange style bearings. I just need to figure out how to chain drive the rollers externally.
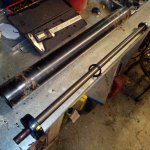
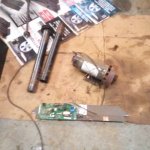
All disassembled. More to come.
I broke my Right Achilles Tendon 2+ years ago and have not ridden any of my 4 BSA motorcycles since. They start easy with the kick starter when warm, but after sitting a few months, they can be a bear to start. Here are a few examples. Most on the market sell in the $1,000.00 range.



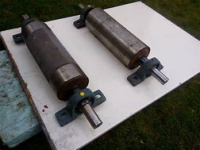
This old tread mill was being thrown out by my daughter during one of her last home sales. I drug it home and it's been in my barn for several years. I left the upper portion in the dumpster and just brought home the roller base.
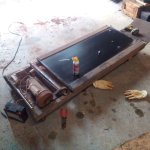
Moving on to the disassembly I discovered the motor is 125 VDC and I think it had died a terrible death. So the only thing I decided to use was the rollers and shafts. They are a 2.5" rollers, that ring like a driveshaft tube. They use a 3/4" shaft with internal bearings, So unlike most of the M/C starters, I won't be using Pillow Block , or flange style bearings. I just need to figure out how to chain drive the rollers externally.
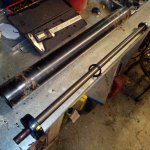
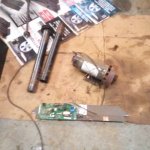
All disassembled. More to come.